All About Ranges
NSSF promotes the development and responsible management of state-of-the-art target shooting facilities by providing leadership in information, communication and partnerships between ranges, industry and community.
First Shots for Your Range
Learn more about NSSF’s highly successful First Shots program and how to leverage it best to attract new customers.
Read MoreRange News
NSSF’s Firearm Industry Jobs
Online employment portal was designed specifically to connect professionals in the firearm industry with the companies that need them. NSSF Members receive discounted rates.
Submit a Job OpeningFirearm Retail and Range Businesses for Sale
The perfect solution for any FFL retailer or firearms range to get the word out - and it is an exclusive resource available for posting only by NSSF members.
List Your Business for SaleFeatured Videos
Introduction to Range Safety and Etiquette
Range Action Specialists
If your range is facing challenges that need immediate attention, if you wish to become more proactive with best management practices or if you’re seeking professional guidance on range design and improvements, our team of Range Action Specialists stand ready to assist you.
Learn MoreSubscribe To Bullet Points
Distributed weekly, NSSF’s Bullet Points is the associations flagship newsletter. Its is a quick-read roundup of what you need to know – the latest industry news, research, legislative happenings and much more.
NSSF Range & Retail Advisory Council
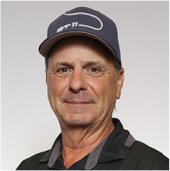
Ed Arrighi
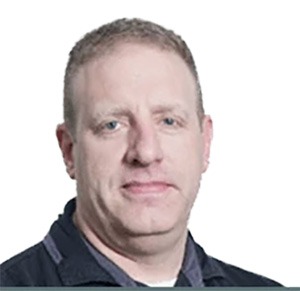
Paul Bastean
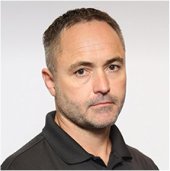
Ryan Burt
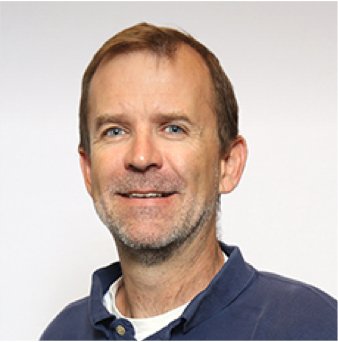
Sean Mahoney
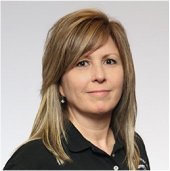
Jeanine Philips
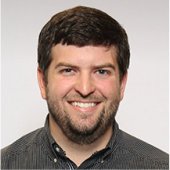
Hunter Simmons
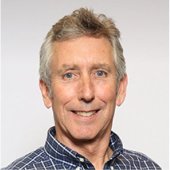
Richard Sprague
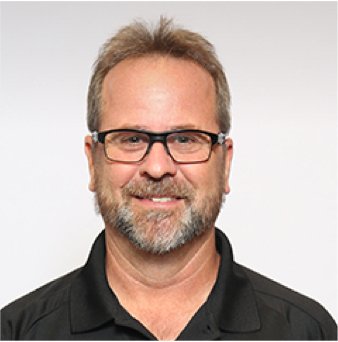
Jeff Wait
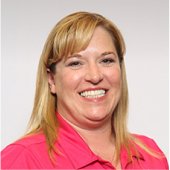
Jeanelle Westrom
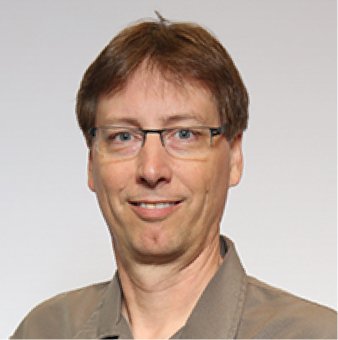
Doug VanderWoude
Become a member of NSSF
With a membership of thousands of manufacturers, distributors, firearms retailers, shooting ranges, sportsmen’s organizations and publishers nationwide, our industry’s voice is strong.
Help us make it that much stronger.
Join Now